APQP Advanced Product Quality Planning
Acceso rápido
Preguntas frecuentes
¿Qué es el APQP y para qué sirve?
El APQP (Advanced Product Quality Planning o Planificación Avanzada de la Calidad del Producto) es una metodología utilizada en la industria manufacturera para asegurar la calidad y la eficacia en el desarrollo y lanzamiento de nuevos productos. Se utiliza principalmente en sectores como la automoción, pero su aplicación se ha extendido a otras industrias.
¿Cuáles son las 5 fases del APQP?
Las 5 fases del APQP son:
- Planificación y Definición: Se establecen los objetivos, responsabilidades y se crea el plan de trabajo.
- Diseño y Desarrollo del Producto: Se definen las especificaciones y se diseña el producto para cumplir con los requisitos del cliente.
- Diseño y Desarrollo del Proceso: Se diseñan los procesos de fabricación y se establecen los controles necesarios.
- Validación del Producto y Proceso: Se realizan pruebas y verificaciones para asegurar que el producto y el proceso cumplen con los requisitos.
- Lanzamiento, Producción y Retroalimentación: Se inicia la producción y se recolecta información para mejorar continuamente.
¿Qué es APQP y PPAP?
APQP (Planificación Avanzada de la Calidad del Producto) es un marco estructurado para desarrollar productos y procesos que cumplan con los requisitos del cliente desde el inicio.
PPAP (Proceso de Aprobación de Piezas de Producción) es un proceso estandarizado para demostrar que un producto y su proceso de fabricación cumplen con las especificaciones del cliente antes de la producción en masa.
¿Cómo hacer un APQP?
Para hacer un APQP, sigue estos pasos generales:
- Forma un equipo multidisciplinario: Incluye representantes de diseño, ingeniería, calidad, compras, producción y otros departamentos relevantes.
- Planifica y define el programa: Establece los objetivos, responsabilidades, cronograma y recursos necesarios. Define los requisitos del cliente y las especificaciones del producto.
- Diseña y desarrolla el producto: Crea el diseño del producto y asegúrate de que cumpla con los requisitos del cliente. Realiza revisiones de diseño y utiliza herramientas como AMEF para identificar y mitigar riesgos.
- Diseña y desarrolla el proceso: Define los procesos de fabricación y establece los controles necesarios para asegurar la calidad. Utiliza herramientas como diagramas de flujo y planes de control.
- Valida el producto y el proceso: Realiza pruebas y verificaciones para asegurar que el producto y el proceso cumplen con los requisitos. Documenta los resultados en un PPAP.
- Lanza la producción y obtén retroalimentación: Inicia la producción y recolecta datos para monitorear el desempeño y realizar mejoras continuas.
Recuerda: El APQP es un proceso iterativo, por lo que es importante revisar y ajustar el plan a medida que se avanza. Utiliza herramientas y metodologías de calidad para garantizar el éxito del proyecto.
¿Qué es APQP?
APQP es una guía en el proceso de desarrollo de un producto y también es una forma estándar para compartir los resultados entre los proveedores y las empresas automotrices.
El APQP (por las siglas en inglés de Advanced Product Quality Planning o Planeación Avanzada de la Calidad de Producto) es un proceso desarrollado a finales de 1980 por una comisión formada por Ford, GM y Chrysler.
Esta herramienta APQP es utilizada hoy en día por estas tres empresas, sus proveedores y algunas filiales.
APQP es el proceso o marco oficial de procedimientos y técnicas requeridas para un sistema de desarrollo de productos en la industria, particularmente en la automotriz y fue desarrollado por la AIAG (Automotive Industry Action Group).
El APQP al igual que el PPAP, AMEF, SPC y MSA son consideradas las Core Tools del sector automotriz y es un requisito de la norma internacional IATF 16949.
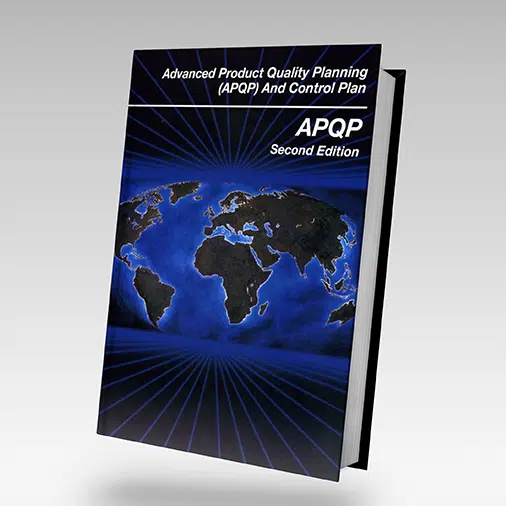
Objetivo del APQP
El APQP es un proceso desarrollado a finales de 1980 por una comisión formada por Ford, GM y Chrysler. Esta herramienta es utilizada hoy en día por estas tres empresas, sus proveedores y algunas filiales. El APQP sirve de guía en el proceso de desarrollo y también es una forma estándar para compartir los resultados entre los proveedores y las empresas automotrices.
Dicho proceso se enfoca en el desarrollo, la industrialización y el lanzamiento de nuevos productos.
Durante estas fases 23 temas son monitoreados, estos deberán estar terminados antes de que la producción en serie inicie. Algunos temas que son monitoreados son: robustez del diseño, pruebas de diseño y el cumplimiento de las especificaciones, diseño del proceso de producción, estándar de inspección de calidad, capacidad de proceso, capacidad de producción, embalaje de producto, pruebas de productos y plan de formación de operadores, entre otros.
Las 5 fases de APQP
Se han definido 5 fases para la ejecución de este proceso. El manual de Core Tools de la AIAG para APQP detalla los elementos de entrada/salida para cada una de ellas. El manual de APQP define las entradas y salidas para cada etapa. Las salidas o entregables de la etapa 1 serán las entradas para la etapa 2 y así sucesivamente. En total la lista de entradas y salidas consta de 49 puntos.
Etapa 1 de APQP: Planificación y definición del programa
Esta fase de APQP nos da una guía para comprender y traducir la voz del cliente, y así, realizar una planeación estructurada del producto o proceso, contemplando las características especiales que permitirán asegurar la calidad.
En esta etapa, se definen los objetivos de calidad del producto, se identifican los requisitos del cliente y se establecen los planes y los recursos necesarios.
Primero, identificamos los objetivos de calidad del producto.
Por ejemplo, se establecerían requisitos para la seguridad, el rendimiento, la eficiencia energética, la ergonomía y el diseño. Además, se identificarían los requisitos específicos del cliente, como la durabilidad, la facilidad de uso.
Las entradas a esta etapa del proceso son:
1.1 Voz del cliente
1.2 Plan de negocios
1.3 Benchmarking
1.4 Suposiciones del producto / proceso
1.5 Estudios de confiabilidad
1.6 Información de cliente interno
Salidas:
1.7 Metas de diseño
1.8 Metas de confiabilidad y calidad
1.9 Lista preliminar de materiales
1.10 Diagrama de flujo preliminar del proceso
1.11 Lista preliminar de características especiales de producto y proceso
1.12 Plan de aseguramiento del producto
1.13 Soporte de la dirección
Otras salidas: listado de contactos clave, cronograma de proyecto, equipos
Interdisciplinarios formados y comprometidos (team feasibility commitment).
Etapa 2 de APQP: Diseño y desarrollo del producto
El APQP aquí nos guía hacia el uso de las herramientas para asegurar la calidad.
En esta etapa, se desarrollan prototipos del producto, se realizan pruebas para verificar su funcionamiento y se evalúan los resultados.
Estas son las salidas de la fase:
2.1 AMEF de diseño
2.2 Diseño para manufactura y ensamble
2.3 Verificación del diseño (Que el diseño cumpla con los requerimientos)
2.4 Revisión del diseño (Que el producto diseñado cumpla los objetivos, por ejemplo, durabilidad, pruebas de rendimiento y pruebas de seguridad).
2.5 Construcción del prototipo / plan de control
2.6 Dibujos de ingeniería
2.7 Especificaciones de ingeniería
2.8 Especificaciones de materiales
2.9 Cambios a dibujos y especificaciones
2.10 Requerimientos de equipos, herramentales y refacciones
2.11 Características especiales de producto y proceso
2.12 Requerimientos de equipos de Inspección y prueba (gages)
2.13 Compromiso de factibilidad / soporte de la dirección
Etapa 3 de APQP: Diseño y desarrollo del proceso
APQP nos permite visualizar y analizar el desarrollo del proceso.
En esta etapa, se validan los procesos de fabricación para asegurarse de que sean capaces de producir el producto con la calidad requerida.
Durante esta etapa, se llevan a cabo los siguientes pasos:
- Desarrollo de la secuencia de producción: se definen los pasos necesarios para producir el producto, incluyendo la selección de proveedores y la planificación de la capacidad de producción.
- Preparación de las herramientas y los equipos: se identifican las herramientas y los equipos necesarios para producir el producto y se preparan para su uso.
- Desarrollo de los procedimientos de producción: se definen los procedimientos necesarios para producir el producto, incluyendo los procedimientos de inspección y control de calidad.
Las salidas en esta etapa son:
3.1 Estándares de empaque (Generales)
3.2 Revisión del sistema de calidad del producto/ proceso
3.3 Diagrama de flujo del proceso (operaciones, inspecciones, flujos).
3.4 Distribución de planta
3.5 Matriz de características
3.6 AMEF o análisis de modo y efecto de fallas de proceso
3.7 Plan de control de preproducción
3.8 Instrucciones de proceso
3.9 Análisis de los sistemas de medición (MSA).
3.10 Estudio preliminar de habilidad del Proceso
3.11 Especificaciones de empaque (Especificas)
3.12 Soporte de la dirección
Etapa 4 de APQP: Validación del producto y proceso
Esta fase de APQP nos guía a verificar y validar los resultados obtenidos de las etapas previas, y de esta forma poder asegurar un buen lanzamiento de producto y/o proceso.
En esta etapa, se lleva a cabo la producción del producto y se verifica su calidad para asegurarse de que se está produciendo con los procesos validados y que se están cumpliendo los requisitos del cliente.
Durante esta etapa, se llevan a cabo los siguientes pasos:
- Inicio de la producción: se comienza la producción del producto utilizando los recursos y los procedimientos definidos en la etapa anterior.
- Validación del proceso: se llevan a cabo pruebas para verificar que el proceso de producción es capaz de producir el producto con la calidad requerida. Estas pruebas pueden incluir pruebas de producción piloto o pruebas de producción a pequeña escala. Normalmente estas pruebas se conocen como “run at rate” o producción a plena capacidad.
Si se identifican problemas durante la validación del proceso, se realizan ajustes para mejorar su eficacia y garantizar la calidad del producto.
Las salidas de esta etapa son:
4.1 Corridas de prueba y validación de producción (Run at rate).
4.2 Evaluación del sistema de medición
4.3 Estudio preliminar de capacidad del proceso
4.4 Aprobación de partes de producción (PPAP)
4.5 Evaluación de empaque
4.6 Plan de control para producción
4.7 Cierre de la planeación de calidad y soporte de la dirección
Etapa 5 de APQP: Retroalimentación, evaluación y acciones correctivas
En esta etapa de APQP, se monitorean los procesos de fabricación y se realizan ajustes para mantener la calidad del producto a niveles aceptables.
También se resumen los aprendizajes adquiridos durante el desarrollo del APQP.
Durante esta etapa de APQP, se llevan a cabo los siguientes pasos:
-
- Emplear gráficas de control u otra técnica estadística para identificar variación de proceso. Analizar y tomar acciones correctivas para reducir variación.
- Establecer mejora continua entendiendo las causas comunes y reducir sus fuentes de variación.
- Asociarse con el cliente para recibir su retroalimentación y hacer los cambios necesarios para corregir deficiencias y asegurar su satisfacción, particularmente en cuanto a producto, entrega y servicio.
- Documentar las lecciones aprendidas en el proceso.
Las salidas de esta última etapa de APQP entonces serán:
5.1 Reducción de la variación
5.2 Mejora de la satisfacción del cliente
5.3 Mejora de la entrega y servicio
5.4 Uso efectivo de las lecciones aprendidas
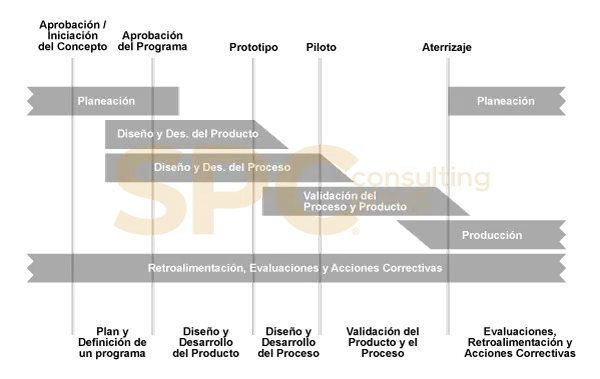
APQP y las Core Tools
A continuación, veremos cuales son las herramientas clave de calidad o Core Tools para cada etapa del APQP:
Etapa 1 de APQP: Planificación y definición del programa
Análisis FMEA (Failure Mode and Effect Analysis): se utiliza para identificar los modos de falla potenciales y evaluar su impacto en el producto y el proceso.
Etapa 2 de APQP: Diseño y desarrollo del producto:
Plan de control de calidad: se utiliza para definir los requisitos de calidad del producto y los procedimientos de control de calidad a seguir durante la producción, que se controlará, quien lo hará, cada cuando, con qué y que hacer en caso de incumplimientos.
Etapa 3 de APQP: Diseño y desarrollo del proceso:
Análisis de Capacidad del Proceso y MSA, Measurement System Analysis: Se utilizan para evaluar la habilidad del proceso para cumplir las especificaciones definidas, así como la precisión y la estabilidad de las herramientas y equipos de medición utilizados en el proceso de producción.
Etapa 4 de APQP: Validación del producto y proceso:
Control Estadístico de Procesos (SPC, Statistical Process Control): se utiliza para monitorear continuamente el rendimiento del proceso y detectar cualquier desviación del comportamiento normal.
Plan de Procesos y Aprobación del Producto (PPAP, Production Part Approval Process): se utiliza para verificar y aprobar que el proceso de producción y el producto cumplen con los requisitos de calidad y los estándares del cliente.
Etapa 5 de APQP: Retroalimentación, evaluación y acciones correctivas:
Análisis de las causas raíz: se utiliza para identificar las causas subyacentes de los problemas de calidad y para desarrollar soluciones de mejora continua.
Conclusiones de APQP
Estas son algunas de las herramientas clave de calidad más comúnmente utilizadas en el proceso APQP, y pueden variar según las necesidades y requisitos específicos de cada organización y de cada producto. Sin embargo, todas estas herramientas están diseñadas para ayudar a garantizar la calidad del producto y mejorar el proceso de producción.
APQP es la guía fundamental para los procesos de introducción de nuevos productos en la industria.
SPC cuenta con los recursos de capacitación y asesoría necesarios para apoyar los procesos de las empresas de nivel global.
Artículo por SPC Consulting Group en colaboración con el Ingeniero Gustavo Gutiérrez.
DERECHOS DE USO: Queda prohibido copiar, reproducir, distribuir, publicar, transmitir, difundir, o en cualquier modo explotar cualquier parte de este material sin la correcta atribución correspondiente o sin la autorización previa por escrito de Servicios Profesionales de Alta Consultoría S.C. (SPC Consulting Group) o de los titulares correspondientes.
Usted deberá citar este artículo copiando y pegando el siguiente texto:
APQP Advanced Product Quality Planning
SPC Consulting Group
https://spcgroup.com.mx/apqp/
Si deseas saber más sobre la herramienta APQP, comunícate hoy con nosotros, o te invitamos a nuestros próximos entrenamientos en diferentes ciudades como Monterrey, Querétaro, Guadajalara, entre otras dentro y fuera de la República Mexicana y en modalidad online desde cualquier ciudad.